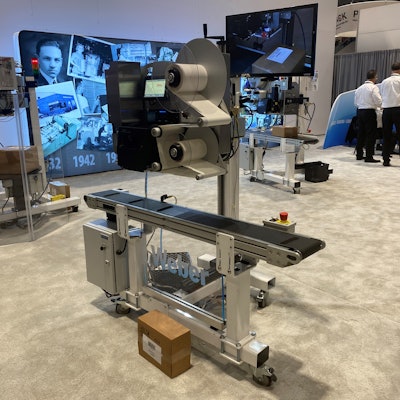
At PACK EXPO International, Weber Packaging Solutions unveiled its latest label printer/applicator, Model 4050, designed with distribution centers and e-commerce operations in mind.
Based on a version of a Weber machine created by its engineers in Germany, Weber’s Model 4050 is engineered to be a modular, variable height labeling system that is easy to service while using 80 percent less air than comparable systems.
Less air, more precision
Weber’s machine combines modulated vacuum technology with integrated sensors that constantly measure the labeling pressure required and make adjustments as needed during the labeling operation. Chris Erbach, integrated marketing manager at Weber Packaging Solutions, says this technology should make the 4050 appealing to distribution centers and e-commerce businesses who need variable height solutions to accurately label packages and envelopes coming in sequence down the line.
“For anyone doing shipping address labeling for different sized packages, this model will sense the height of the box, and bring it down to a quarter of an inch and blow the label on from there,” says Erbach. “It’s a sort of a hybrid — not completely air-free label application, but it uses significantly less air than what is typical in the industry.”
Two compressed air circuits allow the label to stay on the tamp pad and the thruster to stay in position when an emergency stop occurs on the production line. This eliminates the need to reset the applicator when the emergency is cleared and the line restarts. Because it is a no-contact labeling system, Model 4050 can also handle fragile items and even do product labeling, Erbach says.
In addition to its sensor-based variable height labeling technology, Model 4050 features variable-stroke operation and increased precision with powered unwind and rewind modules that minimize wear on the printing modules while ensuring precise printing. The 13.75-in. unwind matches the label length and ribbon length for one-to-one media consumption, thereby reducing downtime and eliminating partial changeovers.
Modularity in mind
Modularity and simplicity are built into the design of the 4050. “We wanted something that was more modular with parts that we could source here in the U.S. to be cost-effective,” says Erbach. Featuring a labeling module designed without service parts, Model 4050 is easy to adapt to particular applications and service, Erbach says. The only maintenance item – the print engine – can be maintained per the manufacturer's requirements. Print engines from all leading manufacturers can be used in the Model 4050.
The labeler's clear cover over the pneumatic system makes it easy to see and access for operation, servicing and cleaning. There are two separate compressed air cycles: one for safety-relevant processes such as moving the tamp, and one for general functions such as label management. Color-coded tubing and LED indicators make it easy to follow the action in busy facilities.
Available in right or left-hand application models, Model 4050 can be configured to handle thermal-transfer or direct thermal label applications, Erbach says. Other standard features on the Model 4050 include a 7-in. LCD color touchscreen for easy operation and diagnostics.