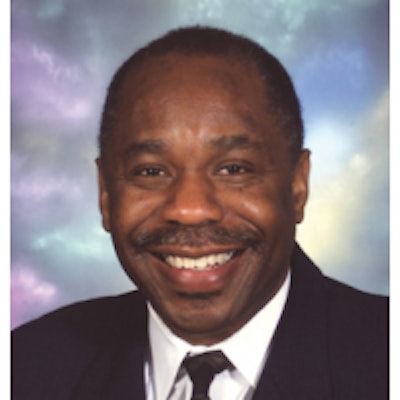
Defective extrusion blow-molded bottles become more problematic the longer they go undiscovered. When discovered at a CPG company’s facility, they can disrupt line operations. When discovered in a CPG company’s distribution network, they add to costs because the filled bottles must be separated. When discovered by the consumer, they can prevent repeat purchases. It therefore benefits a CPG company to be proactive in its approach to troubleshooting.
The starting point should be the design of the bottle. The 2/27/12 Packaging Insights article, Extrusion blow molding, identifies various design-related considerations that facilitate extrusion blow molding. It’s a given that the bottle design must be replicated in the mold cavity; beyond that, the overall quality of the craftsmanship of the mold exerts a strong influence on the frequency and severity of bottle defects.
A proactive approach extends to the selection of the supplier of the extrusion-blow molded bottles. The justification is that quality-assurance not only involves the prevention of defects but also the quick, effective analysis and correction of defects; however, many CPG companies don’t factor in a supplier’s troubleshooting capabilities. The biggest reason likely is an uncertainty about how to evaluate those capabilities—before the advent of defects, rather than after-the-fact.
A CPG company needs to understand that defects can be categorized as either associated with the parison or with the formed container. Thus informed, the company can ask any prospective extrusion blow-molder about how it troubleshoots, relative to each category of defects. Since there are dozens of specific defects within each category, a CPG company should be wary of information overload. To avoid that, a CPG company should emphasize that it’s interested in those defects that—were they to go undetected by the extrusion blow-molder—would cause that CPG company the most problems.
If, for example, the involved product is a liquid, it would be prudent for a CPG company to ask the extrusion blow-molder questions about the causes of leakers and about the associated troubleshooting. One aspect that should arise is the integrity of the weldline (the center line that runs across the bottom of the bottle). A bottle with a defective weldline is a sure leaker, but its cause(s) might not be obvious. Possible causes might lie with the closing of the mold, the pinch-off of the parison, the trimming of the flash (excess plastic), something else, or a combination of the aforementioned.
Distinct from defects that affect a bottle’s performance are those that affect a bottle’s aesthetics. An example is decorative grooves that don’t come in as prominently as designed. Another example is a surface that is supposed to be smooth emerging as rough. A possible culprit is insufficient pressure with which the parison is blown to the contours of the mold (or even the time that the blown parison is held against the contours of the mold).
Yet another type of defect involves the bottle’s neck finish, which can complicate capping operations, including induction sealing. Here, possible causes include misalignment (either of the mold or the blow pin), damage due to the trimming of flash from around the neck finish, and excessive shrinkage around the neck finish.
Despite the diversity among defects, troubleshooting typically leads to an adjustment to one or more core parameters, namely: melt temperature; extrusion speed; blow pressure; blow time; parison drop time (how long parison hangs before the mold closes around it); and parison alignment. Less typically, the defects might be due to how worn the equipment is or even how well the equipment is cleaned and maintained.
Other times, the resin is the problem, in that it contains contaminants, making an extrusion blow-molder’s resin supplier a reasonable subject of inquiry by a CPG company. Even in the absence of that problem, resin suppliers always are eager to convince extrusion blow-molders that troubleshooting can be curtailed by the proper choice of resin, ranging from the traditional “workhorses” to high-performance formulations. And although the choices differ across a variety of characteristics, one that always heads the list is melt strength because of its influence on the formation of the parison.
A CPG company should not be surprised if its questions about an extrusion blow-molder’s troubleshooting capabilities are beyond the knowledge of the sales representative, who often is not a technical specialist. That’s okay, as long as the questions are relayed to the proper personnel and competent responses are given. It’s advisable for such exchanges to be made prior to a visit to the blow-molder’s facility. Even if the visit is purely evaluative—in that no business has yet been awarded to the blow-molder—a CPG company can judge how the previously supplied information is reflected in the observed operations.
With extrusion blow-molding (as with any process), the quality-assurance of supplier and buyer are linked, and the more thorough the troubleshooting by the former the less burden on the latter. Some CPG companies have supplier certification programs wherein the supplier certifies that deliveries will be free of defects, or at minimum, defects will not exceed designated tolerances.
A certification program backed by the requisite controls doesn’t mean that a CPG company should not perform any testing; however, any testing should do what it’s purported to do. An example to the contrary is statistical sampling for the gram weight of bottles, as a troubleshooting measure for impact resistance, proneness to leaking, etc. A bottle of the specified gram weight might, nonetheless, have its weight unevenly distributed throughout the walls of the bottle. A better troubleshooting measure would be statistically sampling dissected bottles and measuring their wall thicknesses, especially in corners. An extrusion blow-molder can control wall thickness by a variety of means, not all of them aimed at uniformity; some bottle designs benefit from having thicker walls in certain areas, achievable by parison programming.
“If you go looking for trouble, you’re likely to find it,” is a warning that many of us received as youths. But when it comes to quality-assurance in general, and troubleshooting in particular, it’s not a warning. It’s the whole idea.
Sterling Anthony is a consultant, specializing in the strategic use of marketing, logistics, and packaging. His contact information is: 100 Renaissance Center- Box 43176; Detroit, MI 48243; 313-531-1875 office; 313-531-1972 fax; [email protected]; www.pkgconsultant.com