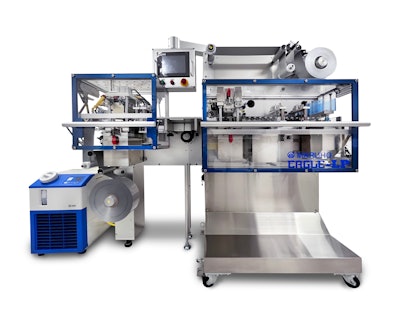
On show was the new Eagle-LP blister machine from Maruho Hatsujyo Innovations (MHI)–the U.S. subsidiary of Japan-based Maruho Hatsujyo Kogyo Co. Ltd. The system is a cost-effective option for development stages, stability testing, and initial small-batch production.
The Eagle-LP addresses two longstanding challenges in early-stage blister packaging: affordability and floorspace. Many pharma manufacturers have faced challenges finding blister units for stability testing, clinical trials, and small batch runs that aren’t prohibitively expensive and unnecessarily lengthy or bulky.
“It's a very small form factor for R&D spaces, small businesses—it’s flexible to install and budget friendly,” said Kazuko Aldrich, general manager, MHI. The Eagle-LP measures just 1.8 meters in both length and height, and just .9 meters in width.
For those in the process of development, smaller equipment without the bells and whistles of full-production systems can speed progress. The base machine accommodates manual infeed, but optional add-ons include cameras, printers, and automated in-feed.
Aldrich explained that the system accommodates a variety of products for blister packaging—liquid, powder, or solid. Importantly, the Eagle-LP is also designed to accommodate a newer generation of more sustainable blister film substrates – ones that are typically more difficult to form and seal. The unit can easily accommodate PVC, PVDC, PET, ACLAR, ALU, and PP. At the show, the booth featured Amcor’s Amsky blister.
The Eagle-LP can run up to 20 cycles/min, with a blister format area of 110 X 60mm and a maximum blister depth of 20mm. It can handle forming materials up to 320mm in diameter, and lidding materials up to 220mm in diameter. The unit is capable of both thermoforming and cold foil forming.
Currently, MHI is featuring a promotion in which customers can obtain customized packaging prototypes at no cost. Shipping for these prototypes is also free.
Related reading: Blister Package Recyclability Meets Machinability