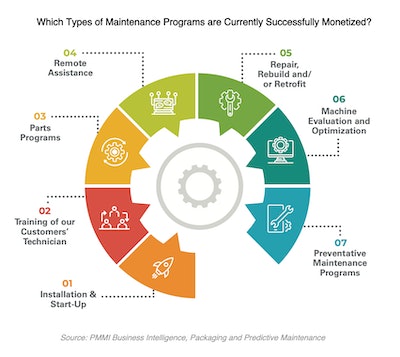
Predictive maintenance is the ability to monitor a machine, or machine component, and avoid unplanned downtime by foreseeing machine failure and allowing the opportunity to take preventative action.
There are two categories of technology that must be implemented to create a predictive maintenance solution, the first being hardware. Smart sensors are usually a key component, and the PMMI Business Intelligence report “Packaging and Predictive Maintenance,” said that a “likely future trend is for processing capacity to be embedded directly on sensors.” Edge computing devices are also used in some advanced predictive maintenance solutions.
In order to decide where to implement smart sensors in a packaging machine, it is important to understand which data is useful. OEMs and integrators who were interviewed said that run-time, current/voltage draw, and speed are the three most useful types of data, however the report points out that run-time may not be reliable for predictive maintenance, as many failures of motor driven equipment happen during the first year due to manufacturing defects or installation error, and not at the latter part of the machine’s life.
The key point is that there is a wide range of data to draw from. The first priority should be to take advantage of any existing smart devices that are already installed in the machine, such as PLCs and variable speed drives. Once sensors are laid out, edge computing devices can be tied into the system, and can decide which data is useful – transmitting only that particular data to the cloud and thereby saving data transfer and storage costs.
After data collection, the second key technology is software and analytics (often hosted on the cloud). Because most machine builders do not possess the ability to write software in-house, a predictive maintenance specialist will often be needed at this stage. Most predictive maintenance hardware solutions come with their own dedicated software; but a single solution that brings all of the data under one umbrella is not yet on the market.
Figuring out how to monetize predictive maintenance can be a hinderance to its adaptation. End users benefit from reduced downtime and increased lifetime of the machine, improvements that will also benefit the bottom line. But for OEMs, a machine with a “radically” extended lifetime also means new business models are necessary to remain profitable over the course of time. The report suggests that a solution is needed that satisfies both group’s needs, and one promising candidate is ‘Machines as a Service,’ or MaaS. This model involves pricing based on performance goals which are set between the end user and the OEM. One example is an OEM whose model involves retaining ownership of packaging machines and charging the customer based on the successful operation of the machine, thereby incentivizing the OEM to minimize downtime and maximize machine lifetime.
Download this FREE report below.
Source: PMMI Business Intelligence, Packaging and Predictive Maintenance