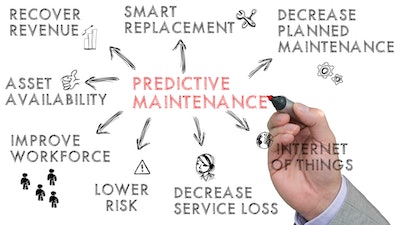
Predictive maintenance is one smaller part of the broad concept of digitalization, or ‘Industry 4.0.’ It refers to the ability to monitor a machine, or machine component, and avoid unplanned downtime by foreseeing machine failure and allowing the opportunity to take preventative action. Since plant downtime can incur losses in the millions of dollars of lost output, an investment in predictive maintenance technology is a logical step.
According to Packaging and Predictive Maintenance, “Developments in predictive maintenance functionality for plant-level software have been taking place the longest. All the major digitalization platforms will offer the ability to perform advanced analytics on data being already collected by existing automation infrastructure; and there are numerous start-ups developing new platforms too.”
There are two areas where predictive maintenance technologies are taking place, and the second area of implementation – the factory floor – may have potential issues with assets that may or may not be connected to an existing infrastructure. Or, the measurements being collected by those that are connected, are not the right data to be most effective at performing predictive maintenance.
To solve this issue, “smart sensors” have become a hot technology in the last 3-4 years. Small MEMS-based devices with integrated wireless communications, and microprocessors that can be placed on existing infrastructure to create new points of asset measurement, they have become more affordable thanks to a broad uptake in consumer applications. Assets can now be retrofitted and monitored in a way never previously possible.
The report found that 29.4% of the packaging and processing industry interviewed are evaluating predictive maintenance technology; 21.6% are piloting it; and up to 23.5% have already implemented it. It is expected that factories that manufacture in batch, such as many food & beverage production operations, will widely adopt this technology, since equipment failures in batch manufacturing can result in the loss of an entire batch. Also good candidates are fast-moving consumer goods companies – with low margins and high volumes – another area where downtime could be “financially catastrophic.”
Primary packaging machines tend to be the most complex, and to have the most demanding requirements made of them by end users, so this level would see the most complicated predictive maintenance solutions. Primary packaging is the first layer of protection - responsible for protecting the product – and in most cases can’t be manually applied if the line goes down, making downtime a much bigger liability than with secondary or tertiary machines.
Download this FREE report below.
Source: PMMI Business Intelligence, Packaging and Predictive Maintenance