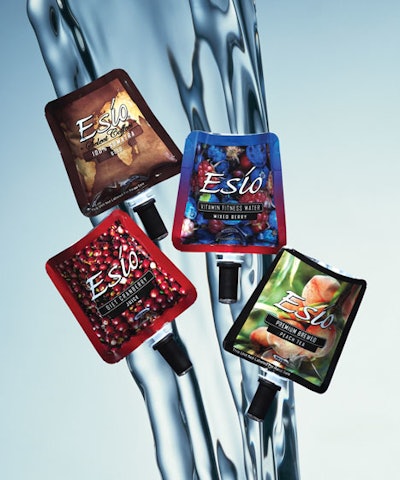
According to its creator, conversations around the water cooler have become much more interesting since the January launch of the new Esio Beverage System from Esio Beverage Co. LLC of Mesa, AZ. An on-demand drink system that provides hot or cold beverages from a selection of 13 concentrate varieties, the Esio Beverage System relies on an innovative pouch with a self-sealing fitment and a disposable pump, along with a custom water dispenser engineered by the company to act as a veritable beverage fountain.
Esio Beverage Co. was founded in 2005 by Frank Leonesio, who is also the founder and CEO of bottled water company O Premium Waters. Leonesio licensed the patented dispensing technology, which Esio calls drop’n drink™, from intellectual property provider Intelligent Coffee Co. (www.iccinnovations.com) to create the Esio Beverage System.
Relates Esio Beverage president Lyle Myers, “We developed the Esio Beverage System to provide the consumer with a fast, easy, convenient, and green [see sidebar below] way to get all of their noncarbonated beverages. There really is no other beverage system on the market today that provides both hot and cold beverages at the touch of a button.” Drink selections include coffee, tea, electrolyte replacement beverages, and more.
Integral to the development of the system and the concentrate package was IPN USA Corp. (www.ipnusa.com) of Peachtree City, GA. IPN is a Netherlands-based flexible-pouch spout and closure supplier that over the years has expanded to provide such complementary services as pouch design and converting, filling equipment, and co-packing services—as in the case of Esio.
Versatile beverage system
The basis for the Esio Beverage System is the drop’n drink technology, which allows users to drop an airtight Esio-Pak™ concentrate pouch into an Esio bottle-fed or reverse-osmosis filter-fed water-dispensing system, press a button, and receive a beverage of their choice.
When the user pushes either the hot or the cold button on the Esio dispenser, water is dispensed from the 1⁄2-gal hot reservoir or the 1-gal cold reservoir at the same time as the concentrate is dispensed from the Esio-Pak through its proprietary dispensing pump. The water and concentrate mix in mid-air within the machine, and the beverage flows from a dispensing nozzle into any size cup, bottle, glass, or pitcher. Because the concentrate mixes with the water in mid-air, explains Myers, there is no opportunity for cross-contamination of flavors when the next user drops his or her beverage selection into the machine.
Once the user has dispensed the desired amount of beverage in the preferred concentration—the machine includes a Strength Selector Dial with 15 settings—the self-sealing pouch can be removed from the system and stored for future use. Each 3-oz Esio-Pak holds enough concentrate to make up to 18 6-oz beverages.
The strength of the concentrate dispensed from the pouch and the Esio-Pak’s automatic reclosability feature are controlled by IPN’s 4-mm Clean-Clic® connector fitment coupled with a custom-designed disposable liquid pump (DLP) from IPN and Intelligent Coffee Co.
As IPN USA director of manufacturing Tom Ferguson explained to Packaging World during a recent visit to the Peachtree City plant, the Clean-Clic is a reclosable fitment that engages with a male probe. When the male probe is inserted, it “locks” into the plug portion of the Clean-Clic, allowing it to reseal the fitment when the probe is retracted. The DLP, which can dispense a wide range of liquids, is designed to lock into place inside the standard 4-mm Clean-Clic (see illustrations on p. 58).
When a pouch is dropped into the dispensing system, a metal ring inside the DLP is activated at a very high rate of speed by a solenoid inside the dispenser. Depending on the position of the Strength Selector Dial, the DLP can open and close anywhere from 35 to 40 times per second. This high rate of activation also ensures that the concentrate does not come in contact with air until dispensing. That, combined with stabilizers in the ingredient list, ensures a 12-month shelf life, even after opening.
A single-source supplier
From packaging materials to final filled and cartoned Esio product, IPN covers all the bases. The Esio-Pak’s Clean-Clic and DLP components are manufactured at IPN’s Houten, Netherlands, facility, using Husky (www.husky.ca) Hylectric injection-molding machines. The components are shipped to IPN’s Peachtree City facility, where they are joined with premade pouches (see sidebar below for more pouch details) that are converted by a strategic partner of IPN India plc. IPN USA then fills the pouches on custom IPN SFA (seal/fill/apply) equipment, manufactured in Houten, and cartons them on a new Adco (www.adcomfg.com) 15D105 cartoning machine.
Before the Esio project, manufacturing operations in IPN USA’s 20,000-sq-ft facility primarily consisted of development engineering of custom applications and the insertion of fitments into premade pouches on six IPN HSM hand-seal machines. “We do not consider contract packaging to be our core business,” says Ferguson. “But this was an opportunity where our customer did not have the capabilities, and so they asked us if we could package the product and essentially tailor it to their needs.”
To ready the plant to co-pack the Esio-Pak pouch, IPN outfitted a 2,400-sq-ft production room with two SFA machines; the first was installed in October 2006, while the second, delivered in December 2007, has not yet been validated for filling. The machines are equipped with custom-built clean-in-place systems connected to a 1,000-BTU gas boiler that cleans, rinses, and sanitizes the fillers between production runs.
Ferguson says that IPN developed the SFA machine to meet the speed requirements of packagers filling preformed pouches at 40 to 60 pouches/min. Vital to the Esio project, in particular, is the machine’s ability to fill the liquid concentrate without introducing oxygen into the process. “The coffees and the teas are by far the most susceptible to oxidation, but you want to limit contact with oxygen for all of the concentrates,” says Ferguson. “Even if it doesn’t cause oxidation, it’s still one more entry point for contamination. So we keep the process as airless as possible.”
Airless filling achieved
During operation, the two-up SFA machine’s dual magazines are loaded with preformed pouches that are open on one end. Two-at-a-time, pouches are picked from the magazine—open-end-up—with lifting arms equipped with suction cups. The pouches are held vertically until sliding horizontal rails grasp the pouches at the top and index them to the first station. On their way to this station, each pouch is printed with a lot number via a Ci700 continuous ink-jet printer from Citronix (www.citronix.com).
At the first station, Clean-Clic fitments, which have been oriented by a vibratory bowl feeder and carried to the station via feeder rails, are picked and placed by two robotic arms into the open end of the pouches. Sealing bars then seal the pouch openings around the fitments. At the next station, cooling bars clamp around the seal area, reducing the temperature.
At the third station, vacuum nozzles are inserted through the Clean-Clic fitments to draw all the oxygen from the pouches. Also at this station, a vacuum test is performed to ensure that all the pouch seals are good. If the pouch fails, it will not be filled at the filling station. At the next station, the pouches are ambient-filled with concentrate by nozzles that descend into the pouches through the Clean-Clic fitments. As the nozzles exit the pouches, they lock the Clean-Clic fitments shut, preventing air from entering.
At the last station, the DLP pumps—their openings protected by a foil label—are picked from a feeder rail by robotic arms and inserted into the Clean-Clic. After DLP insertion, the pouches drop down onto a conveyor below and are carried to an operator who visually inspects them before placing them into a plastic tote.
Semi-automatic cartoning, casing
Filled totes are then transported by conveyor to the 15D105 semi-automatic hand-load Adco cartoner, installed in October 2006. Ferguson says one of the reasons this machine was chosen was because it can be upgraded in-the-field with a barrel cam loader for automatic product loading—a feature that will most likely be utilized as Esio’s volumes continue to increase. During operation of the machine, a high-speed rotary carton feeder picks a carton from the magazine, opens it, and places it onto the machine’s conveyor. Erected cartons are carried past two operators who manually pick filled pouches from a tote and place three into each carton.
The cartons are closed and then sealed by a Nordson (www.nordson.com) ProBlue® hot-melt glue system, after which they receive a lot number from a Macsa (www.macsalaser.com) K-1010 SP laser system. These numbers match those placed on the pouch and later on the master case, for full traceability of the product.
Filled, sealed, and coded cartons are then hand-loaded 28 to a case, which is set on a conveyor that carries it through an Ovalstrapping (www.ovalstrapping.com) Model JP 501 automatic case taper. The case then moves past a ProSeries 768 Marksman ink-jet case printer from FoxJet (www.foxjet.com) that applies the corresponding lot number, as well as the variety description, a bar code, the Esio company name, and a best-by date.
Future awash with opportunity
If all goes as planned for Esio, IPN will be very busy keeping up with the demand for the company’s concentrate. The Esio water-dispensing system is currently offered for free to home and office markets through licensed dealers, when customers agree to purchase a certain number of Esio-Pak concentrate products each month. “That process has really been working well,” says Myers, “because these dealers already have an embedded base of customers that they can convert to the Esio Beverage System.”
Esio-Pak concentrate products are offered through these dealers, as well as on Esio’s Web site, for a cost of $11.99 to $16.99 per carton, or $4.39 to $5.99 per pouch, depending on the beverage variety.
View supplemental photos that correspond to this feature in the
August 2008 issue of Packaging World that details the packaging process
for the new Esio Beverage System.