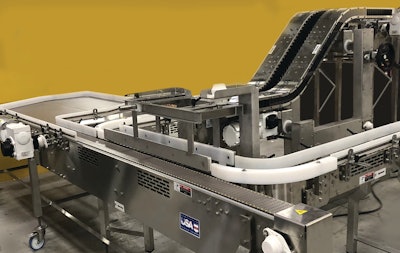
This content was written and submitted by the supplier. It has only been modified to comply with this publication’s space and style.
The conveyor system transports empty cans from bulk accumulation to single file, through air rinse cleaner; checkweigher and X-ray. Product then travels through a liquid rinse/dry onto two 90-degree curves. An operator then chooses to divert product to an attached portable reflow accumulation table or allow cans to elevate, using a gripper incline conveyor in a very small footprint, onto an upper level reflow accumulation table.
Shown in this video, the S-shaped incline gently grips individual units and elevates them to over 5 ft in an incredibly small footprint. Products are gripped gently by the pair of side-by-side parallel conveyors that use neoprene gripper bulb chains to control product, delivering it to an elevated accumulation table. The upper accumulation table allows product to recirculate until it is manually removed by operators for insertion into a retort basket.
A manually operated gate was also installed, prior to the gripper, allowing the customer to reroute product onto a secondary portable line. This section is attached with simple pin-pull and is used to feed a separate recirculating reflow accumulation table upstream of a secondary retort.
Reflow accumulation continually recirculates product until each can or tub is gently guided, to an operator for manual removal. In general, accumulation conveyors provide a means to temporarily store product, allowing additional time or distance ahead of a downstream operation.
Besides Reflow accumulation, Multi-Conveyor regularly builds Alpine, Uni-Directional, Bi-Directional, In-Line, Mass flow, Single file, Multi-Lane, Serpentine, Drum Spiral and Rotary accumulators and tables, along with their associated infeed and discharge systems, to meet customer rate and capacity specifications.