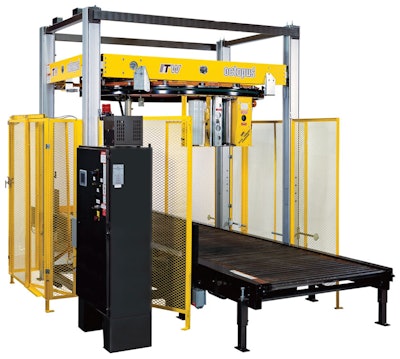
ITW Muller’s customer for this application was intent on minimizing the weight of the stretch film used to secure its pallets. The year before, the company had taken steps to reduce the thickness of its film—a proprietary, high-quality formulation from ITW Muller—from 70 ga to 60 ga. With the addition of the Octopus 303 with OctoMAX technology, its goal was to reduce the amount of film used per pallet by 0.5 oz, down from 2.5 oz. “They had a pretty aggressive goal, and they set that target of getting to two ounces of film per load, while obviously making sure that the loads weren’t toppling over, and the product would arrive at their customers’ as expected,” says ITW Muller business development manager Dan Schmidt.
The OctoMAX system uses proprietary hardware and software to allow for real-time measurement of the pre-stretch performance and film usage for every load produced, ensuring the optimal settings at all times. “It’s designed so that the user can get a text message or an e-mail if too much film is being used, or if it falls out of tolerance,” so the problem can be immediately resolved, explains Schmidt. A Web-based reporting system sends all of the data to a server where it’s documented and stored for historical purposes.
Through a touch-screen control panel, the OctoMAX provides another film-saving feature: It allows for variable film-tension settings, where the operator can program on-the-fly how much tension they want to apply at the beginning of the wrap, during the middle of the wrap, and at the top and at the bottom of the wrap. The Octopus’ pre-stretch technology further maximizes film usage, with up to 300% pre-stretch.
Says Schmidt, “What we see typically with other carriages is that within the first year, they are well below 200 percent pre-stretch. So what we are saying is not only are we giving you this really high-performance pre-stretch, but we are also putting our money where our mouth is and proving it to you on a daily basis.”
In the case of the beverage packager, its application consisted of wrapping loads of 12-oz cans on a pallet measuring 47 in wide x 37 in long x 54 in high. According to information provided on the Greener Package Awards entry form, “in one year, the [Octomax-equipped] line wrapped over 62,000 pallet loads, which resulted in an annual film savings of 1,937.5 pounds.”
Data-wise, ITW Muller reports that the system reduced 121.3 kg/CO2 equivalent per 10,000 packages, according to data produced by a combination of the OctoMAX recordings and ITW Muller’s film plant data, which uses the U.S. EPA Web site greenhouse gas calculator.
Commenting on the technology, Greener Package Awards judge Dean Bellefluer, of D-Idea, says, “Until there is a sustainable alternative to stretch-wrapping, I’m all for optimizing equipment efficiencies. This is a step in the green direction.”