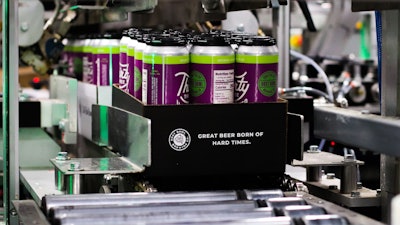
In U.S. history, the Dust Bowl describes a depression-era drought in the Midwest that forced many of its “Okie” inhabitants to migrate from their infertile farms in America’s breadbasket toward California, based on mostly unrealistic promises of employment and prosperity. In John Steinbeck’s classic novel The Grapes of Wrath, protagonist Tom Joad leaves Oklahoma on an ill-fated hero’s journey that at times is pretty dark, even by today’s standards. But it’s also a hopeful depiction of resourceful people who leaned on each other to survive hard times in search of a better life for their children.
Brett Tate is one of those Californians who traces his family’s heritage back to the Dust Bowl. When the retired teacher turned entrepreneur opened a new brewery venture in 2009 in Turlock, Calif., he named it Dust Bowl Brewing Company as an homage to this history.
Out of the gate, Tate secured a local rising star in craft brew circles to be his brewmaster. He hired Don Oliver, also from Turlock, who was the winner of the 2006 Samuel Adams Longshot Homebrew competition. By 2009, the aptly named Hops of Wrath IPA, among other brews, first came to market in Dust Bowl’s brewery and taproom. The cleverly named Hops of Wrath IPA was the first beer produced by Dust Bowl Brewing Co., a nod to Steinbeck’s novel The Grapes of Wrath, about the historical Dust Bowl.
Pandemic shakes format mix
Then, in early 2020, another mass migration—this time the pandemic-induced consumer shift away from restaurants, bars, and taprooms—shook the craft brew landscape. But production didn’t need to slow down if Dust Bowl could recalibrate its packaged product mix to accommodate a new reliance on retail. At that point the brewery’s increased focus on canned beer distribution was not just on-trend, but necessary for survival. In this wide-angle photo of the packaging line, we can see an accumulation table ahead of a PakTech can handle applicator, Bevco conveyance, and a DMM case/tray packing in the background.
“We were able to switch gears and pump out more cans, but it took some work,” Oliver says. “We only had a small Codi Manufacturing canning line than ran at 50 cans a minute when we were running 12-oz cans. That was a great line and it did well for us, but it wasn’t going to keep up with the number of cans that we needed to produce after the onset of COVID-19. When you’re trying to drain 200-barrel brite tanks, 50 cans a minute is pretty slow.”
Trying to keep up with canning is what led Oliver to approach David Weller at Pacific Packaging Systems Inc. (PPSI), a line integrator specializing in craft brew, in search of faster can output. But footprint was an initial hurdle. A 30,000-sq-ft facility seems like plenty of space, but a lot of that was tied up in the brewing process and an existing bottling line.
“We were trying to squeeze all this new canning equipment into a small space, and I knew it was not something we were going to be able to achieve on our own, so we reached out to David [Weller] at Pacific,” Oliver says. “I think we went through around 18 or 20 design iterations to figure out how we were going to put all the equipment in. Our bottling line from CFT was taking up the entire packaging area, and we needed to canibalize some of its footprint. The bottling line had the classic horseshoe-type shape, so the idea we came up with was to chop the line at the bend, flip the horseshoe the other direction and tighten it up, and then squeeze all the new canning equipment into the space we’d freed up.”
That strategy did the trick. Armed a the new canning line that it can grow into, the brewery hopes to nearly double its production over the coming years, from 22,000 barrels in 2022, to a goal of nearer 40,000 down the road.
The new line
For the heart of the canning line, Oliver and Weller landed on a KHS Innofill CAN Compact 18-valve rotary monoblock filler with rotary seamer, capable of filling and seaming well over 200 cans/min. The system handles 12-, 16-, and 19.2-oz cans with minimal changeover.
“KHS seemed like a good fit for us for the [low lead time] timeline, for its compact size, and for the cleanliness of the machine. We heard some nightmare stories about seamer cleanliness and other issues on some others that we’ve seen,” Oliver says. “We’ve had to make a couple of programming modifications. Also, we got rid of the bubble breaker because we didn’t feel it was really helping us with dissolved oxygen, and it was more of a contamination risk. So, we eliminated that and then we saw some benefits there. Now it’s running at around 210 cans per minute at max speed for 12-oz printed cans.”
Can formats that require label application, or larger 16- or 19.2-oz cans that require can handle multipack applications instead of cartoning, are slowed to between 90 to 180 cans/min to accommodate their respective downstream operations. More on that shortly.
With that much increased filling firepower, an almost entirely new packaging line would be required. However, a few accessory items from the original line still operate today, including a CODI depalletizer and triple-twist rinse conveyance at the front of the line.
“Coming off the CODI depalletizer, we have a larger, full-sweep conveyor that was supplied by conveyor supplier Bevco. From there, it goes to a single filer that travels back into the CODI for the twist rinse, and we place an air ionizer on whichever lane we’re using to feed the KHS monoblock filler.”
After filling and seaming, cans get a quick rinse and travel single file through a Filtec machine to confirm fill-height and reject non-conforming fill levels. A block inverter then flips cans over for bottom date and batch code on a Videojet CIJ coding and marking system.
“Once it gets the date code, it goes through another inverter, and a blower to dry off the top. The conveyor then passes through the labeler, a Pack Leader USA 501. If we’re adding labels to brightstock, we’ll set it up and slow everything down for the label job. Printed cans will run right through the unengaged labeler at full speed.” Pairs of labeled 6-pack multipacks with PakTech can handles applied are packed in high-walled 12-count trays on DMM equipment.
Once past the labeler, 12-oz cans are diverted toward a DMM carton erector and cartoner, which side-pushes cans into a 12-pack erected carton format, applies adhesive to the flaps, and closes the cartons. Dust Bowl has the change parts for a 16-oz 8-pack, but seldom uses this format. Filled and seamed bright stock cans get a Filtec fill-level check prior to date coding and labeling.
Larger 16- and 19.2-oz cans aren’t cartoned. Instead, they receive HDPE can handles from a PakTech machine. This compact equipment can apply handles to 180 larger-format cans/min. Once can handles have been applied, the 4- or 6-can multipacks travel on a small conveyor that bypasses the DMM cartoning machine and ends up punching right into the inlet of another DMM machine, this time a tray former and packer. Most trayed can formats are of 24 cans in either 4- or 6-packs, with one exception.
“For the 19.2-ounce cans, we chose to go on a 12-pack format tray,” Oliver adds. “It’ll get two 6-packs of PakTech-applied multipacks pushed into a smaller 12-pack tray with a higher wall. We’ve got a good relationship with a local company out of Modesto, California called Pacific Southwest Container. They provide us with all our all our board, so all the cartons and all the trays come from them.”
End-of-line packaging
Conveyance carries the three most common pack formats—12-pack cartons of 12-oz cans, 24-pack trays of larger or labeled brightstock cans, and on occasion, 12-pack trays of 19.2-oz cans—to palletizing and pallet wrapping. Both are done on a TopTier TT-L20 Low Level palletizer that comfortably handles four pallets per hour max filling speed of 210 cans/min. A TopTier two-in-one palletizer and stretch wrapper anchors Dust Bowl’s end-of-line packaging operations.
“We had looked at a couple of other models, and we couldn’t find anything that was going to fit within our footprint and within our budgetary constraints, and then TopTier was able to take care of both of those issues,” Oliver says. “The footprint is really small. And price-wise, it’s incredibly competitive.”
The (almost entirely) new canning line at Dust Bowl “is enough to get us quite a ways down the road, as far as production goes,” Oliver says, adding there’s no current need to make further improvements to can filling operations. “I think this canning line is enough to get us up to that 40,000-barrels-a-year mark. We hit a little over 22,000 barrels last year, in 2022, so we still have plenty of room to grow into this line. And even though growth isn’t what it used to be, we grew 4.5 percent last year. Any positive makes us happy considering what we’ve seen out in the market; there’s a lot of uncertainty right now. We’ll hope for the best and plan for the worst, knowing this new canning line gives us the runway and capacity to grow cans even further.” PW