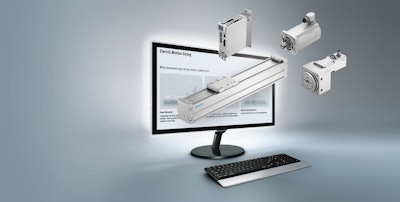
This content was written and submitted by the supplier. It has only been modified to comply with this publication’s space and style.
The Electric Motion Sizing tool improves project efficiency by reducing the engineering time required for identifying and specifying harmonized electric motion systems. Multi-axis handling systems can be specified with Electric Motion Sizing’s sister productivity tool Handling Guide Online, which offers similar benefits.
Festo developed Electric Motion Sizing because it recognizes that machine builders need solutions that help bring products to market faster with less engineering and purchasing overhead. Electric Motion Sizing compresses hours of toil down to minutes.
With this free online productivity tool, users simply input key parameters, such as mass, stroke/travel distance, and cycle time (see video). It performs the complex mass moment of inertia calculations. The tool identifies in real time the combination of components most effective for the application’s parameters. Up to five optimum solutions and motor curves are presented for consideration. The specified components work together, so interoperability is not a concern. Designers can fine tune the selected system by choosing encoder type, brake, and mechanics.
Following selection, the Electric Motion Sizing tool transfers the selected combination of components to the Festo online shop, together with commissioning files. The online shop provides pricing and delivery information. The seamless process from configuration to order is an additional time saver.
Festo integrated Electric Motion Sizing with the Festo Automation Suite for simplified commissioning. With the Festo Automation Suite, diverse products from remote IO to pneumatic valve terminals, PLCs, and servo drives are commissioned via a single free tool. Automation Suite automatically connects to the Festo cloud to download project specific documentation and updates within the software. It also incorporates Codesys code for programming PLCs and motion controllers.