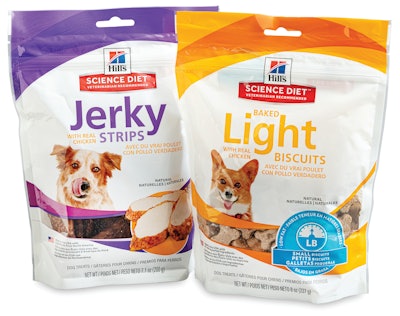
The other 2020 Flexible Packaging Achievement Award Winners are: Innventure's AeroFlexx (Highest achievement) | UFlex Ltd.’s 4D Bag with Handle | UFlex Ltd.’s FlexiTube | Amcor Healthcare’s Insura Seal Verification | Printpack’s Paqui Tortilla Chip Pouch | Amcor Flexibles’ Predilecta Sacciali Jar Shaped Pouch | Glenroy’s Premade Standcap Inverted Pouches | ePac’s Skratch Labs Mosaic Packaging | Printpack’s Stacy’s Women’s History Month Package | Paxxus’ StreamOne | Silver Winners
This award-winning standup pouch for pet treats is made from one of the Thrive™ line of sustainable packaging materials from Plastic Packaging Technologies. Varieties within the new Thrive line are designed to be either recyclable, compostable, or notable for their percentage of Post-Consumer Recycled content. In the case of this particular award winner, a bottom-gussetted standup pouch for 8 oz of Hill’s Pet Nutrition pet food treats, it’s Thrive-Recyclable™ that is being recognized.
Topeka, Kan.-based Hill’s is a Colgate-Palmolive company. It will launch the treats in the new package, which has a double-track reclosure feature from Presto Products, in Q1 of this year. Hill’s also plans to use the Thrive material in larger pinch-bottom bags and large lay-down bags, too.
The significance of this material is best appreciated by first reviewing the multi-layer laminations that are usually used for pet food treats, whose makeup requires packaging materials having good oxygen and moisture barriers, not to mention grease resistance as well. Typically included in such laminations are materials like aluminum foil, polyvinylidene chloride, polyester, or nylon. But while these materials are terrific at delivering performance characteristics like toughness, barrier, machineability, and economics, they make recycling challenging because they consist of too many incompatible materials.
Thrive-Recyclable, by contrast, is described by PPT as monomaterial PE. According to Dave Potter, VP Technical and Engineering at PPT, it’s a two-layer lamination, and the two substrates are married by way of a solvent-free adhesive on a Nordmeccanica laminator. The outside layer is a clear 1-mil high-density polyethylene supplied by Jindal Films. PPT reverse prints this substrate in eight colors on a W&H flexo press. The inner layer is a five-layer blown coextrusion of PE resins. Included in the coextrusion, which PPT purchases from Charter NEX, is EVOH for gas barrier purposes as well as sealant layers. Also important in this coextrusion is the presence of a compatibilizer technology from Dow called RETAIN. Without this Dow component, EVOH is not compatible with the PE recycle stream. But with it, the two incompatible materials mix and distribute evenly. Go to pwgo.to/5466 for more on Retain and its use in the award-winning Bear Naked package from Kellogg Co.
PPT’s Potter says his firm had to bring in all new Totani pouch converting equipment for this material. “The big challenge is heat management,” he says. “Remember, in a more traditional structure, where a 48-ga polyester is the outer layer, the material has a much higher heat resistance. You drive the heat through that outer layer of polyester to activate the polyethylene sealant layers, which have a lower seal initiation temperature. Then, once the seal is made, the sealing jaws are still able to open without sticking to the outer layer of polyester. But with this material, we have an outer layer of polyethylene. That makes it tricky to deliver enough heat for the inner sealant layers to be activated without also melting the outer layer of polyethylene. So this wasn’t just a matter materials development. We had to modify existing pouch-making equipment by adding cooling bars and so forth. It’s an entirely new film technology where materials, equipment, and process all had to come together.”
When asked about the economics of the new material, Potter is reluctant to throw out a number because there are so many variables involved, including the size of package, what barrier properties are needed, and how many pouches are ordered. But when pressed he says materials in the Thrive line will carry a premium of anywhere from 15 to 25% compared to the multilayer alternatives they are designed to replace. It remains to be seen how many brand owners will pay such an upcharge. But Potter likes his chances for two reasons. First, brand owners of all stripes are more serious than ever about setting sustainable-packaging goals and then meeting them; using this material could go a long way toward helping them accomplish their objectives. And second, recycle-ready solutions for flexible packaging offered to brand owners in the recent past have come with an upcharge more like 35 to 50%. That could make the premium they pay for Thrive materials seem downright manageable.
Peter Fallat, Director of Global Design & Packaging at Hill’s Pet Nutrition, says the use of this innovative new material is part of parent company Colgate’s broader sustainability strategy, “a key part of which is getting into recyclable materials wherever technology allows us to.” The pet treat product set to debut in the new material will continue to be packaged on semiautomated equipment at the contract manufacturer where it’s currently packed.
A final note on the Hill’s launch. Use of the How2Recycle logo on the back of the package has been approved by the Sustainable Packaging Coalition. This logo will give consumers two important pieces of information: the pouch is “Recyclable if Clean & Dry” and it is suitable for “Store Drop-off.”