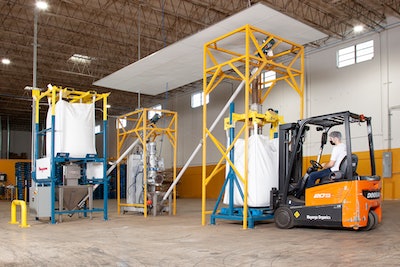
Mayorga’s roasting and packaging plant in Miami, Florida.
Mayorga has already streamlined part of its process by purchasing directly from these farmers, bypassing supply chain complexities and simultaneously striving to alleviate systemic poverty through the direct trade of artisanal organic foods in Latin America.
“We produce a product that is sustainable, not only for the planet, but for the people growing it as well,” says Erin Dall, president and COO of Mayorga.
Mayorga Organics produces and sells organic coffee and other products sourced directly from local farmers in Latin America.
Mayorga coffee offerings.
To accomplish this task, Mayorga installed a bulk handling system comprised of two bulk bag dischargers, three flexible screw conveyors, and a bulk bag filler, all from Flexicon. The system was installed when the new facility was built in 2019.
![]() | BevTech 2022: Driving Sustainability Best Practices Forward in Beverages |
From roaster to grinder to packaging
The flexible screw conveyor at left transfers roasted coffee beans from the bulk bag discharger to the grinder, while the conveyor at right moves ground coffee to the bulk bag filler.
The flexible screw conveyor (top front) transfers beans to the grinder, from which a second flexible screw conveyor moves ground coffee to the bulk bag filler (rear).
The discharger houses a bulk bag spout interface chute with an integral access door. With the bulk bag in position, the operator opens this door to gain access to the bulk bag spout tie. Once the spout has been untied, the access door is closed while roasted beans are discharged from the bulk bag. At floor level, an operator attaches bulk bag straps to Z-Clip strap holders of a bag lifting frame held in position by a forklift.
The beans flow from the bulk bag into an 8 cu ft floor hopper, which charges a 15-ft model 1350 flexible screw conveyor inclined at 45 degrees to feed the grinder. The 3.5-in. diameter enclosed conveyor tube prevents product and plant contamination. The inner screw is the only moving part contacting material and is driven by an electric motor positioned beyond the point at which coffee beans exit the conveyor, preventing material contact with seals.A forklift loads the lifting cradle with suspended bulk bag onto the discharger’s receiving cups.
From the grinder, ground coffee gravity discharges into a 4 ft3 floor hopper that charges a second 15-ft, 3.5-in. diameter flexible screw conveyor, this one equipped with a spiral designed to efficiently propel the fine-ground material to a Flexicon model BFB bulk bag filler.An operator opens an access door and pulls the bag outlet spout through the sealing ring before untying the spout's drawstring.
A palletized open-top bulk bag is placed inside the filler frame, which can be adjusted to accommodate bulk bags ranging from 36- to 72-in. high. Strap hooks, mounted on each of the four corners of the fill head, hold the bag open and stabilize it during filling.
Filled bulk bags are forklifted into a second discharger which unloads coffee into an 8 ft3 floor hopper charging a 15-ft long, 2-5/8-in. diameter flexible screw conveyor to feed the packaging line. The flexible screw conveyor transfers ground coffee from the grinder through downspouting to the bulk bag filler.
Bag strap hooks hold the bag open and stabilize it during filling.
Minimized manual labor and other benefits
The bulk bag discharger unloads ground coffee into a floor hopper, charging a flexible screw conveyor that feeds the packaging machine.
The bulk handling system improves productivity and plant cleanliness, according to Dall. “Flexicon provided a solution that fits within our space limitations, allows immediate packaging, and provides for future production expansion,” says Dall.
![]() | unPACKed with PMMI: Next Stop PACK EXPO International 2022 |