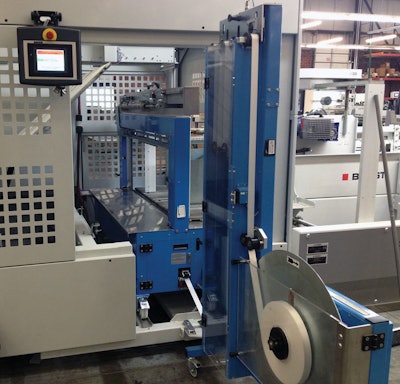
Packrite LLC, High Point, NC, is a converter/finisher for high-graphic corrugated packaging, folding cartons, and fluted blister cards. The company can customize its products and services to meet exacting user needs, including printing, laminating, die-cutting, folding, gluing, and building in carton window features for product visibility. Serving this diverse market requires meeting equally diverse and sometimes difficult design and construction challenges.
On a business trip to Europe, Packrite owners Michael and Mary Drummond planned a visit to Bobst, a Swiss company well-known for its packaging and labeling equipment expertise. The Drummonds wanted to explore the latest gluing equipment innovations that could accommodate their company’s increasing need for versatility. During that trip, they serendipitously discovered something they hadn’t been looking for—the Model US-2000 Transit Line Ultrasonic banding system manufactured by ATS-Tanner Banding Systems of Switzerland, distributed in the U.S. by Wexler Packaging Products, Inc. Packrite purchased an ATS Automated Banding System and a Bobst Streampack batch collector and Bobst Masterfold 170 folder/gluer with double gyro box gluing feature as a package deal.
Going outside of the box
Packrite had typically bundled carton flats in corrugated cases and then put the cases on pallets that were stretch-wrapped for shipment. In December 2013, technicians from Bobst, along with Wexler technicians, installed the ATS Automated Banding System for zero damage bundling and integrated it with the Streampack batch collector and Masterfold folder/gluer, creating one fully automated turnkey solution.
This new straight-to-the-pallet bundle banding system has allowed the company to eliminate the cost and time involved in corrugated casing/gluing operations and also reduced shipping costs per pallet.
Drummond says, “We now are using 30-mm-wide white foamed polypropylene film banding that acts like gentle but durable gift wrapping for our customers. The banding helps us get close to one-third more product per pallet and saves our customers money. For one particular application, I estimated that switching to banding and going straight to the pallet was saving the customer more than $1 million per year by eliminating outer corrugated case packaging material costs, allowing 33% more bundles per skid, and reducing freight weights. Additionally, we have not sacrificed any degree of product protection during shipment. In fact, we have experienced less carton flat deformation and graphics marring by discarding the overall confining and compressing outer corrugated cases in favor of the wide, thin banding. In that regard, to further enhance shipping protection, we also have developed our own corrugated corner board system that helps square-up and secure the banded, stacked bundles on the pallets.”