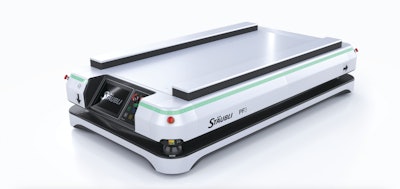
Probably the smallest category of robots in use by packaging operations are autonomous guided vehicles (AGVs). While AGVs have been in manufacturing facilities for years, companies are increasingly turning to autonomous mobile robots (AMRs) for internal transport solutions. Says PMMI’s 2022 business intelligence report on robotics, “Eighty-two thousand AMRs shipped in 2021, with shipments predicted to reach over 600,0000 by 2025.
“More adaptable, flexible, and cost efficient than AGVs, AMRs are being used to navigate dynamic environments and transport a variety of items, from raw materials to finished products. The newest generation of sensors and AI-driven data are making AMRs flexible enough to be easily redeployed and smart enough to navigate a facility without the need for guided wiring or magnets.”
![]() | Read related article from Packaging World’s 2022 Robotics Report, “AMRs Offer Transport Efficiency in Packaging Operations.” |
For packaging operations, AMRs can be used for materials transport, including pallet loads of packaging materials, as well as machine loading. Systems that feature an industrial robot on top of a mobile platform can help with optimization of material flow and packaging processes. Mobile robots’ ability to move around the plant floor also offers production flexibility, as the units can travel among various packaging workstations and perform relevant work at each one.
In August 2022, Packaging World reported on one CPG and private-label packager, Snak King in City of Industry, Calif., that not only installed 16 robotic palletizers, but also three intelligent automated vehicles (IAVs) to transport pallets through the facility from stretch wrapping to warehousing. The company selected IAVs from Quest, a product brand of ProMach, that are equipped with a lidar, or light detecting and ranging, system to move throughout the facility.
![]() | Read related article, “End-of-Line Automation Reduces Snak King’s Labor Pains.” |
Snak King acquired the new robotic palletizers and IAVs to ease workforce shortages and to optimize its throughput capability. According to the company, the three IAVs have replaced 10 to 12 forklifts and have reduced the “chaos” that previously characterized its production floor, while at the same time being safe for workers.
Packaging Robotics: Epson Robots' VT6L-DC All-in-One 6-Axis Robot
Features of the robot include a built-in controller, a reach of up to 900 mm, and a payload of up to 6 kg in a compact footprint. It also comes equipped with two development environments: Epson RC+ for full-featured, easy-to-learn programming and Epson RC+ Express for no-code programming. With the introduction of the VT6L-DC, Epson unveiled a version of its Epson RC+ Express with increased functionality.
Says Epson, “Ideal for automation novices with little to no programming experience, Epson RC+ Express offers a simple, visual-based teaching environment, an easy-to-follow, block-style format, ready-to-use templates, and other time-saving features to get Epson SCARA and 6-axis robots up and running fast.”
Previously available only on select Epson robots, the intuitive software now works with hundreds of Epson SCARA and 6-axis robots. The software is equipped with time-saving features such as Epson proprietary Focus Assist technology with auto-generated fields for quick and easy setup and a built-in 3D simulator to help visualize and fine-tune applications.
“As more businesses implement automation to address workforce challenges, Epson recognizes that more users require not only easy-to-use applications but also the flexibility to be mobile,” says Scott Marsic, group product manager, Epson Robots. “Epson is committed to providing a simplified automation experience. Solutions like the VT6L-DC empower warehousing, logistics, and machine tending operators to move a traditional 6-axis robot from place to place rather than mounting it in a single, stationary location. And, with simple, visual-based programming software like RC+ Express, users can get their robotic automation solutions up and running quickly.”
Packaging Robotics: ROEQ’s ROEQ TMC130 top module and cart system
Says ROEQ Managing Director Michael Ejstrup Hansen, “For customers looking to automate tasks such as quickly moving smaller, lighter cargo between workstations or shelves—even in narrow spaces where larger carts are challenged—this is an ideal solution.”
Like other ROEQ cart systems, the TMC130 can dock to the cart from both ends and offers the flexibility of free space pick up and drop off, enabling it to adapt to almost any workplace. The TMC130 includes mounting holes on the top module for accessories like light towers. There are also mounting holes on the cart to make it easy to adapt for crates and shelving.
The TMC130 has been designed to comply with relevant safety standards, and it comes with ROEQ Assist software for easy and consistent setup with the Omron mobile robot. The new cart and top module system works with Omron’s own panel and has six wheels for easy maneuverability. A side laser kit is also available for increased obstacle avoidance.
Packaging Robotics: Stäubli Robotics’ PF3 AGV platform
The low-profile PF3 operates within very narrow spaces on the factory floor, easily maneuvering around obstacles and carrying out tasks with a positioning precision of ±5 mm. In addition, smart features offer future-proof production and a streamlined workflow.
The PF3 uses standard software interfaces, while an all-around LED strip and 45-deg inclined touch panel provide an ergonomic operator experience. To ensure safety, the AGV is equipped with a 360-deg human safety scanner, five emergency stop buttons, a collision avoidance sensor, and an LED strip that communicates the AGV’s status.
Stäubli adds that the PF3 is also easy to own and maintain. It uses a “drawer” maintenance concept, which means parts are easily accessible from the sides of the AGV and can be changed in minutes. It is built on the company’s patented drive unit and constructed of industrial-proof components, which Stäubli says delivers outstanding performance in terms of productivity as well as total cost of ownership. PW
![]() | Read Packaging World’s complete robotics report, “Robots 2023: Smarter, More Adaptable & More Robust.” |