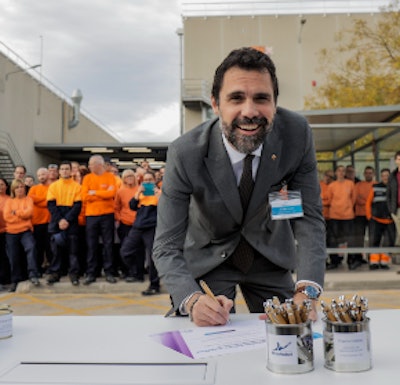
This content was written and submitted by the supplier. It has only been modified to comply with this publication’s space and style.
The new facility, which is expected to be operational by mid-2025, will create around 40 new jobs and has been designed according to the best possible eco-efficiency standards.
Jim Kavanagh, Director of AkzoNobel’s Industrial Coatings business, says the new facility will help the company respond to a strong need from the packaging industry. “The Vilafranca plant will allow us to offer leading-edge products to any customer and country in EMEA, responding to the most stringent bisphenol regulations in force in Europe. The investment is in line with our view that bisphenols of any kind are no longer required to create safe coatings.”
The announcement follows the recent launch of next generation coatings technology including the first two products in its new Accelstyle range. This further illustrates the company’s commitment to giving customers the tangible support they need to transition to a new future: “Both new products – Accelstyle 100 and 200 – can be seamlessly introduced into existing production processes, allowing can makers to transition to coatings that are free from materials of concern, while remaining as commercially viable as possible,” Kavanagh continues.
“The new technology we’ve developed can also reduce carbon footprint by around 30% compared with current epoxy alternatives, highlighting the fact that bisphenol-free metal packaging isn’t just circular, it also meets consumer expectations for sustainable packaging.”
The new Accelstyle products are designed for the exterior of conventional two-piece aluminium beer and beverage cans and are free from bisphenol, styrene and PFAS (per- and polyfluoroalkyl substances). They follow on from the May 2023 launch of Accelshield 700 – the first BPA-NI* (Bisphenol A non-intent) internal coating for beverage can ends – which complies with US Food and Drug Administration (FDA) and EU regulations.
AkzoNobel’s approach to the bisphenol transition of metal cans prioritizes consumer safety and sustainability with responsible material substitutions, while taking care to limit disruption to the value chain. The company is continuing to work closely with customers to help accelerate the adoption of bisphenol alternatives.