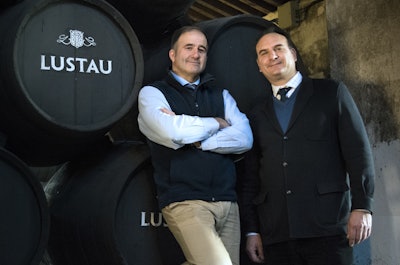
Founded in 1830, Spanish, family-owned business Luis Caballero S.A. produces world-renowned wines and spirits that are exported to 50 countries worldwide. At its winery, located next to the historic Castle of San Marcos in Santa Maria Port, 135 employees produce 7 million bottles of product every year, generating an annual turnover of more than $59 million.
Due to food safety regulations, such as the BRC Global Standard, Caballero must be able to trace its products back to their origin. Therefore, prior to distribution, the company codes each bottle with a batch or date code, along with the time the wine or spirit was filled.
“We have to guarantee the traceability of our products—the batch and date code on the bottle must be easy to read and indelible,” says Jaime Pindado, Technical Manager at Caballero Group.
Caballero has an extensive product range with multiple lines of premium products in glass bottles of different sizes and shapes. Prior to installing a laser coder on its wine bottling line, the company had to adjust its line throughout the day for different print parameters. “This included frequent and long durations of downtime and the potential for product rejects or scrap due to inaccurate coding and poor code placement,” explains Pindado.
Since installing a Domino D320i, these problems have been solved, with manufacturing stops and adjustment times eliminated.
Laser printer eliminates downtime
The printer previously used to code bottles of Caballero’s Lustau wine range used ink-jet technology to print on the bottle label. According to Pindado, because of the different bottle sizes and shapes, the printer needed to be adjusted to accommodate each different one in order to print in the correct field of the paper label.
“Each time an adjustment was required, the line needed to be shut down, with one operator setting the printer adjustment,” he explains. “This downtime meant loss in production and reduced equipment efficiency.”
To alleviate this issue, the company switched to laser technology, selecting a machine from Domino due to its positive experience with the supplier’s equipment. Nearly two decades ago, the company installed its first Domino laser coder on a spirits bottling line to code bottles for its orange brandy liquor Ponche Caballero. Says Pindado, “It has coded more than 100 million bottles in this time, and I do not remember production ever having to stop because of an issue with it—it’s been faultless.
“We wanted the same results on our wine bottling lines. Our previous coding system not only caused significant downtime for realignment, but it also could only print within the label. So we made a collective decision to change to a system that could print clear, concise, indelible codes directly onto the glass bottle. We analyzed several different lasers, but it was Domino’s D320i that provided the best option for us.”
Installed in 2017, the D320i features a modular design and an adjustable iTech scan head measuring 776 x 140 x 180mm, which Pindado says allows D-Series lasers to be installed in the most restrictive places. He notes that the head can be rotated through 90-deg steps to allow for several mounting positions, “and because it is so much smaller, it can easily fit where bigger lasers cannot.”
The i-Tech scan head is also fast—135 bottles/min at Caballero. This is due to its optimized mirror and software control plus its patented RapidScan technology. RapidScan improves the ability of the D-Series to code difficult-to-mark materials and to print longer or more complex codes where more energy or time is required to scribe the code. According to Domino, the technology makes the laser 20% faster than other scribing lasers for high-speed applications.
“This technology from Domino helps us ensure the code can be printed on the glass of the bottles and gives us a speed advantage, thanks to the optimum configuration of the mark field,” Pindado says.
TCO calculated
According to Pindado, the laser printer was also easy to install and learn. “Despite the narrow spaces and complex setup of some of our lines, the D320i was simple to fit,” he says. “Staff immediately adapted to the laser thanks to the intuitiveness of the TouchPanel and QuickStep user interface. It took less than a day of training for them to understand how to operate it, and the Domino team was and still is always available to answer any questions.”
Maintenance is also simple versus Caballero’s previous ink-jet technology. The laser needs minimal intervention, as there are no fluids involved for replenishment or cleaning. The only type of regular maintenance required is exchanging the filters of the fume extraction system, which captures contaminants such as gas and dust that are set free by the laser process.
Given its speed and flexibility, the D320i has notably improved Caballero’s productivity and total cost of ownership. Pindado calculates it like this: “Caballero is bottling 2,500 manufactured orders per year. With our former printers, we used to adjust them for coding the batch onto the glass around 10 times per day. Adjusting the printer to correct the positioning of the code on the label would take three minutes each time, meaning the printer had to be stopped for around 100 hours per year.
“Now, with Domino’s laser technology, we have reduced the downtime of the production line by 90 percent. We have achieved a significant increase in productivity and have reduced downtime to zero due to the print-head cleaning and the costs of the inks. If we make a quick estimation, taking into account the lifetime of the equipment, consumables, and downtime savings, we have improved the TCO drastically.”