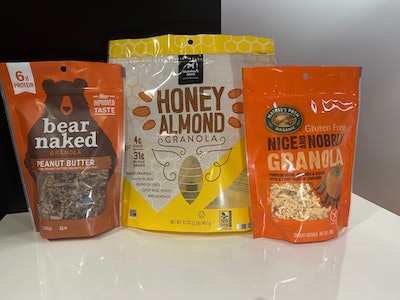
Converters of flexible barrier packaging operate by a simple idea: if a monolayer material can’t provide the barrier, go with a multilayer material. Depending on the need, barrier properties protect against the entry or the exit of elements. The way to describe a multilayer material is from-outermost-to-innermost. Each layer serves a function. The following three examples illustrate that point.
Our first example is paper/polyethylene/foil/polyethylene. The paper provides a printing surface. The foil provides the barrier. The first polyethylene bonds paper and foil, and the second polyethylene is for heat sealing. Applications include bags and pouches for powders and other dry goods.
Our second example is polyester/foil/polyethylene. The polyester carries the print. The foil—as always when present—is the barrier. The polyethylene is the heat seal. Among the applications is a stand-up pouch, with straw, for kids’ drinks.Sterling Anthony, CPP
Example three is polyester/foil/nylon/polypropylene. The polyester is printable. The foil is the barrier. The nylon lends toughness. The polypropylene is the heat seal. This is a structure for a retort pouch (aka the flexible can). Its most suitable application is for low-acid, low-particle foods.
The three examples not only demonstrate different structural complexities but also different processes that must be endured. Foil was part of each example because it’s the ultimate barrier, not overlooking that other materials can provide barrier, subject to the need(s). All three examples cite a polyolefin as the seal, but in other instances, sealing is due to coatings and adhesives. And although the three examples are packages, another application is lidding for modified-atmosphere packaging (MAP) trays and for pharmaceutical blister packs.
Converters differ in terms of equipment and methodology, but they have certain characteristics in common. One is that they are roll-fed, roll-wound operations. Another is that their facilities are laid out in stations. Commonalities aside, converters compete on the basis of their individual capabilities. In other words, given a set of requirements for flexible barrier packaging, offerings can and do differ across converters.
Even when the offerings are the same in terms of materials and the number of layers, they can differ in thickness and in the means by which they are combined. Continuing the point, two structures containing polypropylene can differ, with one using oriented polypropylene and the other one using non-oriented. A similar example lies in the different densities of polyethylene.
When competing offerings provide equal performance, how should a customer decide? Major among possible tie-breakers is price, influenced by the converter’s cost. A particular converter might enjoy a cost advantage owed to a variety of reasons. Quantity purchase discounts with material suppliers is one. Another one is the technology—for example, whether coextrusion or lamination is used in creating the material. Yet another is the number of stations involved. And always a factor is operational efficiency.
But price isn’t everything, and in a best-case scenario, one gets what one pays for. A customer that does not go with the lowest bidder can justify the decision for a variety of reasons. The chosen converter, for example, might have the most experience in supplying the customer’s product category. That same converter has the required production capacity. The converter has better delivery terms and inventory policies. Or perhaps, the converter has a better reputation.
The foregoing discussion notwithstanding, the evaluation of a converter always can benefit from a visit to the converter’s facility. Attention should be paid to the converter’s warehousing of materials and supplies. After all, their integrity can’t be divorced from that of the finished goods. Then there is the housekeeping on the production floor. The construction of multilayer flexible barrier packaging proceeds along a fixed path, and at no juncture should the packaging be exposed to drips or other contamination.
On a different note, sometimes the need is for brawn and beauty, which affects the types of materials and the number of layers. Decisions and trade-offs might be required. A customer might prefer that graphics be in gravure, for example, but an otherwise acceptable converter is equipped for flexography. As another example, reverse printing, which shields the graphics from surface scuffing, might need to be done on a layer of a certain color, such as white, for optimal contrast. At other times, overcoats and lacquers are needed to impart the desired aura.
Steering the discussion to flexible barrier packaging’s sustainability credits, the long-played card is that it’s lightweight. That property translates to lower transportation costs and less vehicular usage. There’s also a favorable packaging-to-contents ratio.
The flexible barrier packaging converting industry, however, is busy improving upon those inherent advantages. Converters are innovating for greater source reduction, devising ways to combine ever-thinner materials. Those converters also are meeting the challenges associated with thinner materials. They include being able to unwind, pull, and rewind those materials at tensions that don’t break the web, while not unduly slowing production rates. In short, barriers are being overcome in the flexible barrier packaging converting industry, for the betterment of all.
Sterling Anthony, CPP, consults in packaging, marketing, logistics, and human-factors. A former faculty member at the Michigan State University School of Packaging, his contact info is:100 Renaissance Center, Box-176, Detroit, MI 48243; 313/531-1875; [email protected].